This article describes the differences in both environment and system requirements, compared to a commercial or office network and introduces DataMax® Extreme cables.
Industrial Ethernet Topology
Most proprietary industrial control systems signal at Kbit rates, thus 10Base-T and 100Base-T Ethernet offer a huge increase in signaling speeds. Ethernet systems used in offices are well accepted, non-proprietary, high-speed, reliable, and easily migrate to even higher speeds. These same benefits are driving Ethernet controls into industrial environments, additionally providing factory-floor data to the enterprise in real time. However, most commercial or office Ethernet hardware cannot survive the rigors of the factory floor. They must be redesigned. Although the signaling protocol is similar, both the cabling media and active gear must be protected from harsh conditions.

The graphic above is a simplified topology diagram that illustrates where Industrial Ethernet (IE) begins and how it interconnects with the existing office infrastructure. The campus or building network contains generic connectivity that may include Category 5e and 6 systems with fiber-optic, copper, backbone, horizontal, wiring closets, patch panels and patch cord components. This generic category cabling extends to the last Telecommunications Outlet (TO). At that point the office environment ends and the IE environment begins.
Generic cabling in an office is not stressed by the ambient conditions or environment. However, the apparatus cabling and everything beyond the network interface (NI) point will be exposed to hazards. Exactly what the hazards are depends on the industrial system being controlled. An automotive robotics welding assembly line, a petrochemical refinery, a food processing facility, or a sports stadium present very different hazards; all of which can destroy commercial grade cabling.
Industrial Control Requirements
Like commercial applications, industrial networks will have a combination of copper, fiber, and wireless infrastructure; but all must be hardened. Unlike commercial environments, industrial process plants are often reconfigured and there is generally no requirement for a 20-year warrantee. Instead, emphasis is placed on elimination of down-time and system reliability, because if a control system shuts down, an entire process plant stops, leading to losses of thousands of dollars per minute.
Specifications called “MICE” tables have been drafted by TIA’s 802.9 Industrial Ethernet committee. These define Mechanical, Ingress, Chemical, and Electromagnetic conditions for three different environments. Many conditions or hazards are defined, some of which are:
- Dust and particles
- Water and humidity
- Temperature
- Sunlight and UV
- EMI
- Oils and chemicals
- Vibration and acceleration
- Flexing — Tear and cut-through
To survive these conditions, small hardened switches or routers with few ports may be bolted to a column close to the control points, connections are minimized, patch cords tend to be short, and the wiring closet becomes very small or disappears.
Network service, connector termination, and system reconfigurations must be done on the plant floor by electricians, not trained technicians. Also, since it will be years before IE migrates to 1000Base-T or higher speeds, reliable Category 5e infrastructure is all that is usually needed. Furthermore, since 10Base-T or 100Base-T only use 2-pair of a customary 4-pair cable; why not use 2-pair connectivity? This minimizes potential failure points and allows a more reliable connector design.
Copper Cables and Connectors
Apparatus cabling and cord sets must also be hardened and protected. Assemblies use encapsulated RJ-45 or cylindrical M12 connectors. The 4-pin M12, used for years with industrial control systems, has recently been adapted for Ethernet transmission. Newer 8-pin versions will now allow both 2-pair and 4-pair UTP cables to be used.
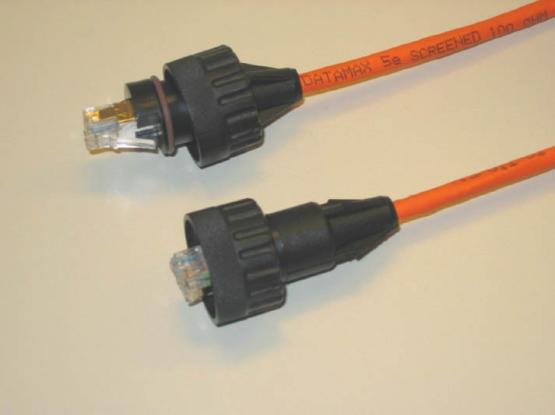
These connector designs use O-rings, over-molding, and/or sealing gaskets to bond to the cable jackets. These techniques provide a mated connection that resists fluids, dust, vibration, and other hazards, yet often may be field assembled. The ideal designs are IP67 rated, assuring resistance to both fluid and dust particle penetration.
Quabbin Wire recently introduced DataMax® Extreme cables for application in harsh Industrial Ethernet applications. These cables are available with either industrial-grade PVC, polyurethane or FR-TPE jacketing material, in 2-pair or 4-pair versions. The jackets are “pressured” over the cable core, locking the pairs in place and allowing over-molding. This results in designs that withstand mechanical abuse, vibration, and impact. For DataMax® Extreme jacket comparison information visit page 18 of the Harsh Environment catalog.